影响增碳效果的因素
(1)增碳剂粒度的影响 增碳剂吸收率的高低取决于增碳剂溶解扩散速度和氧化损耗速度的综合作用。在一般情况下,增碳剂颗粒小,溶解速度快,损耗速度大;增碳剂颗粒大,溶解速度慢,损耗速度小。增碳剂粒度大小的选择与炉膛直径和容量有关。一般情况下,炉膛的直径和容量大,增碳剂的粒度要大一些;反之,增碳剂的粒度要小一些。
(2)增碳剂加入量的影响 在一定的温度和化学成分相同的条件下,铁液中碳的饱和浓度一定。在一定饱和度下,增碳剂加入量越多,溶解扩散所需时间就越长,相应损耗量就越大,吸收率就会降低。
(3)温度对增碳剂吸收率的影响 原则上铁液温度越高,越有利于增碳剂的吸收溶解,反之,增碳剂难以溶解,增碳剂吸收率降低。但是铁液温度过高时,增碳剂虽然较容易充分溶解,但是碳的烧损率会增加,终导致碳含量降低,增碳剂总体吸收率降低。一般铁液温度在1460~1550℃时,增碳剂吸收效率好。
(4)铁液搅拌对增碳剂吸收率的影响 搅拌有利于碳的溶解和扩散,避免增碳剂浮在铁液表面而被烧损。在增碳剂未完全溶解前,搅拌时间长,吸收率高。搅拌还可以减少增碳保温时间,使生产周期缩短,避免铁液中合金元素烧损。但搅拌时间过长,不仅对炉子的使用寿命有很大影响,而且在增碳剂溶解后,搅拌会加剧铁液中碳的损耗。因此,适宜的铁液搅拌时间应以保证增碳剂完全溶解为适宜。
(5)铁液化学成分对增碳剂吸收率的影响 当铁液中初始碳含量高时,在一定的溶解极限下,增碳剂的吸收速度慢,吸收量少,烧损相对较多,增碳剂吸收率低。当铁液初始碳含量较低时,情况相反。另外,铁液中硅和硫阻碍碳的吸收,降低增碳剂的吸收率;而锰元素有助于碳的吸收,提高增碳剂吸收率。就影响程度而言,硅大,锰次之,碳、硫影响较小。因此,实际生产过程中,应先增锰,再增碳,后增硅。
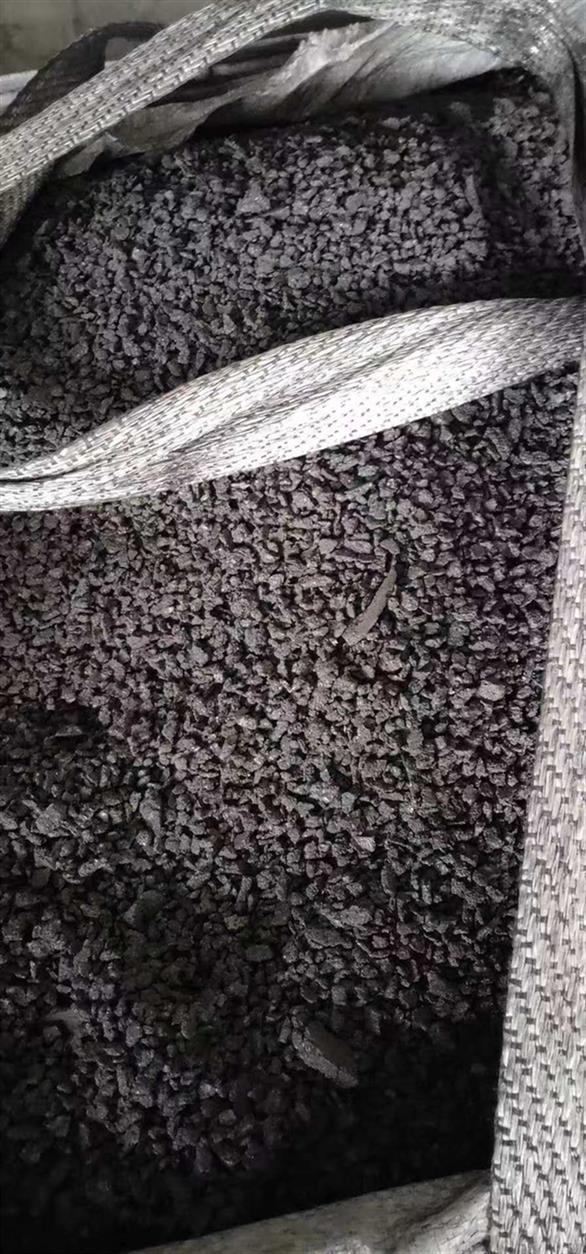
增碳剂在铸造时使用,可大幅度增加废钢用量,减少生铁用量或不用生铁。绝大多数增碳剂都适用于电炉熔炼,也有少部分吸收速度特别快的增碳剂用于冲天炉。电炉熔炼的投料方式,应将增碳剂随废钢等炉料一起往里投放,小剂量的添加可以选择加在铁水表面。
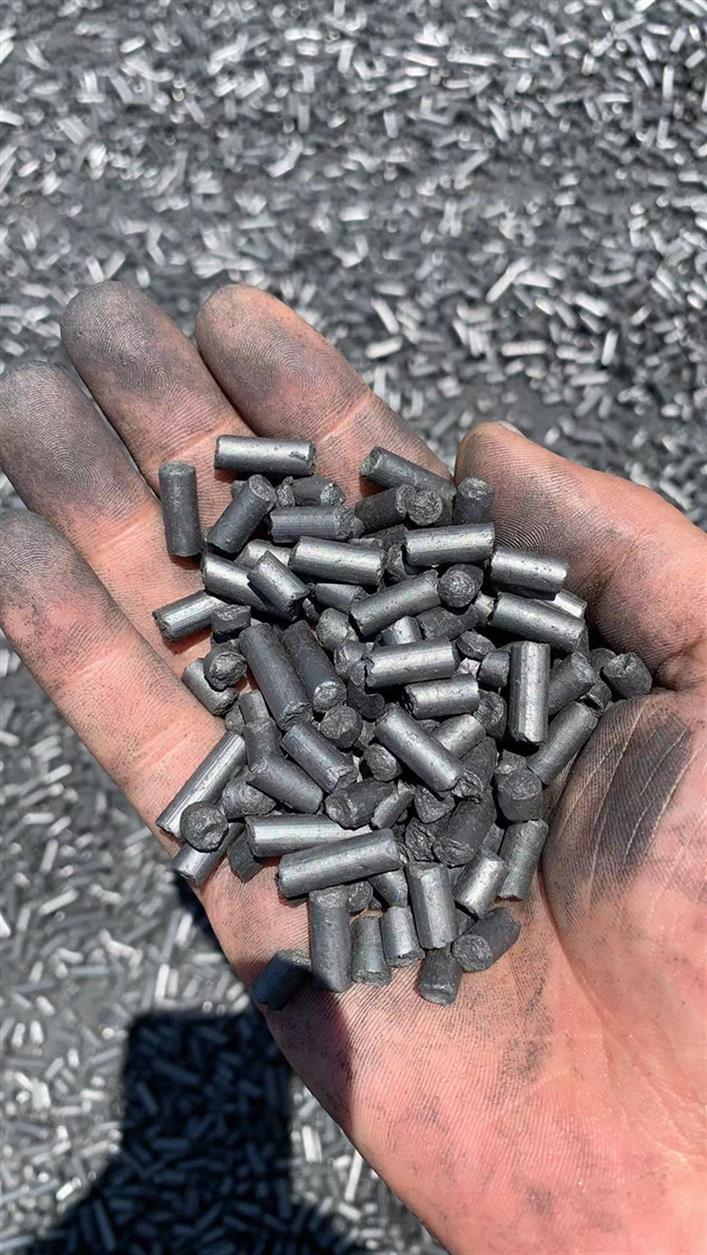
增碳剂的原料有很多种,生产工艺也各异。并非市面上说采用石墨粉剂经压制成型,这种生产方式需要添加过多的粘结剂成型,含碳量一般达不到增碳剂的要求

⑴促进石墨化的工艺措施是减少铁液收缩的好措施。
电炉熔炼:增碳技术的应用是解决铁液收缩的关键技术。由于铁液凝固过程中的石墨析出产生石墨化膨胀作用,良好的石墨化会减少铁液的收缩倾向,因此,增碳技术是好的工艺。
由于加入增碳剂提高了铁液的石墨化能力,因此,采用全废钢熔炼加增碳剂的工艺,铁液的收缩倾向反而较小。这是非常重要的一个观念转变,传统的观念是认为多加废钢会铁液的收缩倾向,这样我们就容易走入一个误区,不愿意多用废钢,而喜欢多用一些生铁。
多用生铁的缺点是:生铁中有许多粗大的过共晶石墨,这种粗大的石墨具有遗传性,如果低温熔炼,粗大的石墨难以消除,粗大的石墨从液态遗传到了固态,使凝固过程中本来由于石墨析出应该产生的膨胀作用削弱,因此使铁液凝固过程中的收缩倾向,粗大的石墨又必然降低了材料的性能。因此,与用废钢增碳工艺相比,大量用生铁的缺点就是:①强度性能低。同样成分做过对比试验,性能低半个排号。②收缩倾向大。同样条件下,比废钢增碳工艺收缩大。
对于电炉熔炼,增碳技术的**是使用的增碳剂。采用废钢增碳工艺,增碳剂就成为增碳工艺中重要的环节。增碳剂质量的好坏决定了铁液质量的好坏,增碳工艺能否获得好的石墨化效果,减少铁液收缩,主要取决于增碳剂:① 增碳剂一定要选用经过高温石墨化处理的增碳剂。只有经过高温石墨化处理,碳原子才能从原来的无序排列变成片状排列,片状石墨才能成为石墨形核的好**,促进石墨化。②好的增碳剂含硫都非常低,w(S)小于0.03%是一个重要的指标。
对于冲天炉熔炼:高温熔炼是关键的技术指标,高温熔炼可以有效消除生铁粗大石墨的遗传性。高温熔炼可以提高渗碳率,减少配料中的生铁加入量。以渗碳方式获得的碳活性好,要比多加生铁带来的碳有较好的石墨化作用,反映在铸件上,就是石墨的形态较好,分布较均匀。石墨的形态好,就会提高材料的性能,包括切削性能,而 石墨化效果好,就能减少铁液的收缩倾向。
//www.megaginasio.com